3.2. Two-dimensional fluidized bed, Two-fluid Model (TFM)¶
This tutorial shows how to create a two dimensional fluidized bed simulation using the two-fluid model. The model setup is:
Property |
Value |
---|---|
Geometry |
10 cm x 30 cm |
Mesh |
20 x 60 |
Solid diameter |
200 microns (\(200 \times 10^{-6}\) m) |
Solid density |
2500 kg/m2 |
Gas velocity |
0.25 m/s |
Temperature |
298 K |
Pressure |
101325 Pa |
3.2.1. Create a new project¶
On the main menu select
New project
Create a new project by double-clicking on “Blank” template.
Enter a project name and browse to a location for the new project.
When prompted to enable SMS workflow, answer No, we will use the standard workflow for this tutorial.
Note
A new project directory will be created in the location directory, with the name being the project name.
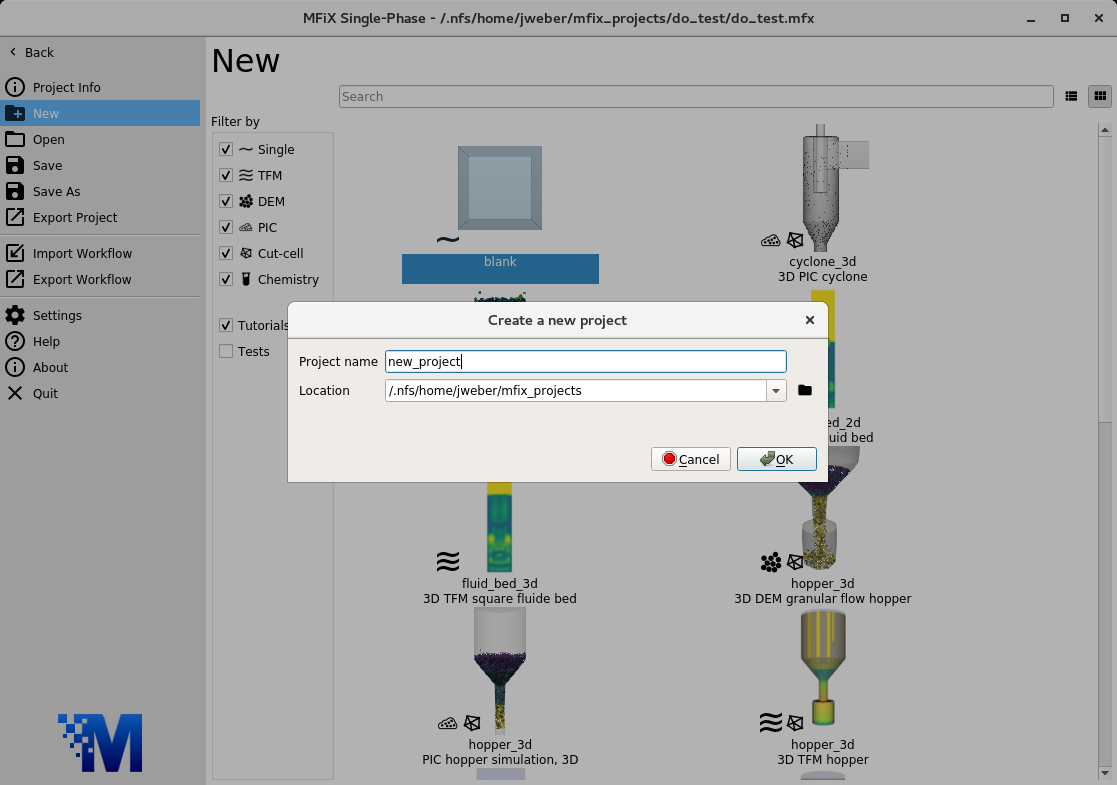
3.2.2. Select model parameters¶
On the Model
pane:
Enter a descriptive text in the
Description
fieldSelect “Two-Fluid Model (MFiX-TFM)” in the
Solver
drop-down menu.
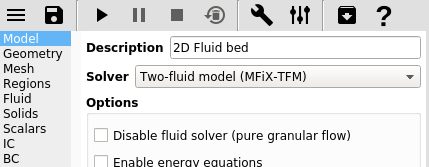
3.2.3. Enter the geometry¶
On the Geometry
pane:
Select the
2 Dimensional
checkboxEnter
10/100
meters for the maximum x valueEnter
30/100
meters for the maximum y value
Note
We could have entered 0.1 and 0.3 to define the domain extents, but this example shows that simple mathematical expressions (+,-,*,/) are allowed.
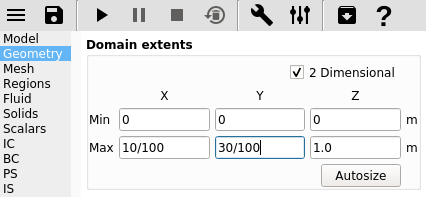
3.2.4. Enter the mesh¶
On the Mesh
pane, Background
sub-pane:
Enter
20
for the x cell valueEnter
60
for the y cell value
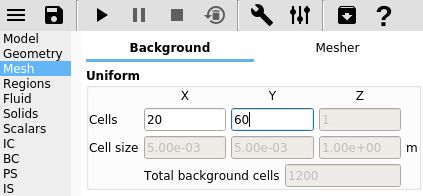
3.2.5. Create regions for initial and boundary condition specification¶
Select the Regions
pane. By default, a region that covers the entire domain
is already defined. This is typically used to initialize the flow field and
visualize the results.
Click the
(add) button to create a new region to be used for the bed initial condition.
Enter a name for the region in the
Name
field (“bed”)Change the color by pressing the
Color
buttonEnter
xmin
ormin
in theFrom X
fieldEnter
xmax
ormax
in theTo X
fieldEnter
ymin
ormin
in theFrom Y
fieldEnter
ymax/2
ormax/2
in theTo Y
fieldEnter
zmin
ormin
in theFrom Z
fieldEnter
zmax
ormax
in theTo Z
field
Note
Here we could have entered numerical values for the coordinates, but it is recommended to use parameters (xmin, xmax etc.) when possible. These parameters will update automatically if the “Domain Extents” change.
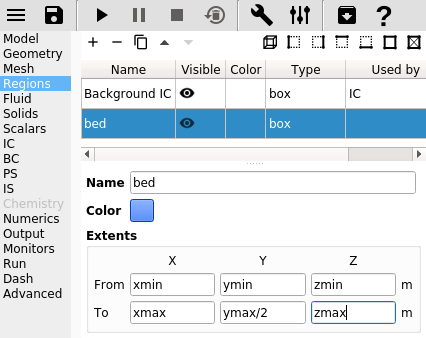
Click the
(bottom) button to create a new region with the
From
andTo
fields already filled out for a region at the bottom of the domain, to be used by the gas inlet boundary condition.From Y
andTo Y
should equalymin
, defining an XZ-plane.Enter a name for the region in the
Name
field (“inlet”)
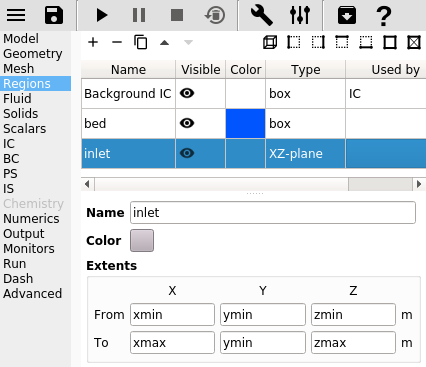
Click the
(top) button to create a new region with the
From
andTo
fields already filled out for a region at the top of the domain, to be used by the pressure outlet boundary condition.From Y
andTo Y
should equalymax
, defining an XZ-plane.Enter a name for the region in the
Name
field (“outlet”)
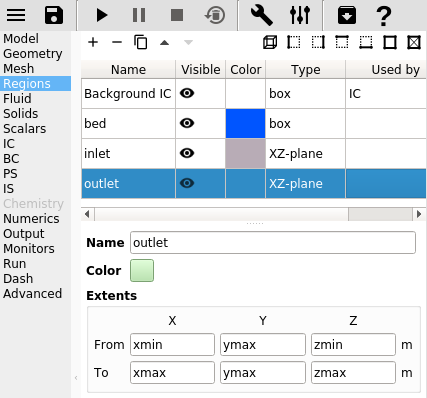
3.2.6. Create a solid¶
On the Solids
pane:
Accept the radial distribution setting (Carnahan-Starling)
Enter a descriptive name in the
Name
field (“glass beads”)Keep the model as “Two-Fluid Model (MFiX-TFM)”)
Enter the particle diameter of
200e-6
m in theDiameter
fieldEnter the particle density of
2500
kg/m2 in theDensity
field
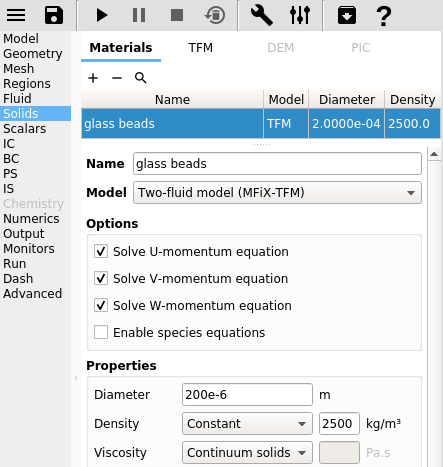
3.2.7. Create Initial Conditions¶
On the Initial conditions
pane:
Select the already populated “Background IC” from the region list. This will initialize the entire flow field with air.
Enter
101325
Pa in thePressure (optional)
field
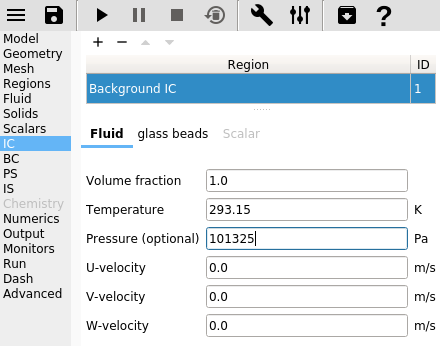
Select the bed region created previously for the bed Initial Condition (“bed” region) and click the
OK
button.
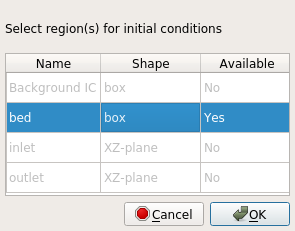
Select the solid (named previously as “glass beads”) sub-pane and enter a volume fraction of
0.4
in theVolume Fraction
field. This will fill the bottom half of the domain with glass beads.
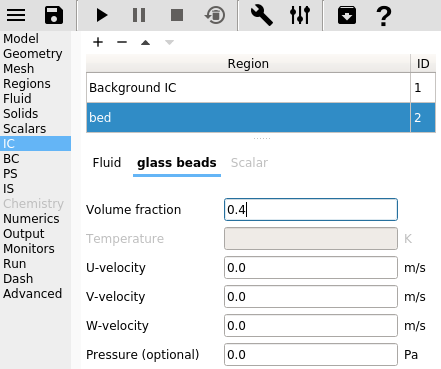
3.2.8. Create Boundary Conditions¶
On the Boundary conditions
pane:
On the
Select region
dialog, select “Mass Inflow” from theBoundary type
drop-down menuSelect the “inlet” region and click
OK
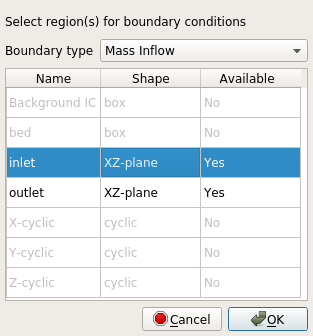
On the “Fluid” sub-pane, enter a velocity in the
Y-axial velocity
field of “0.25” m/s
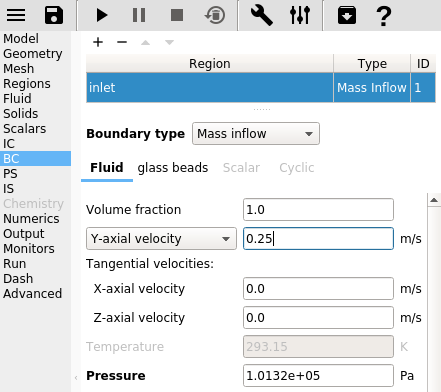
On the
Select region
dialog, select “Pressure outflow” from theBoundary type
combo-boxSelect the “outlet” region and click
OK
Note
The default pressure is already set to 101325 Pa, no changes need to be made to the outlet boundary condition.
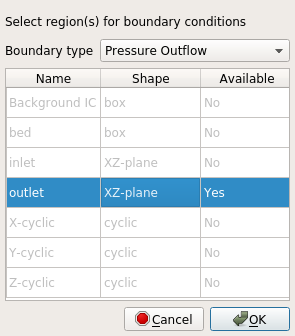
Note
By default, boundaries that are left undefined (here the left and right planes) will behave as No-Slip walls.
3.2.9. Change numeric parameters¶
On the Numerics
pane, Residuals
sub-pane:
Enter
0
in theFluid Normalization
field.
3.2.10. Select output options¶
On the Output
pane:
On the
Basic
sub-pane, check theWrite VTK output files (VTU/VTP)
checkbox
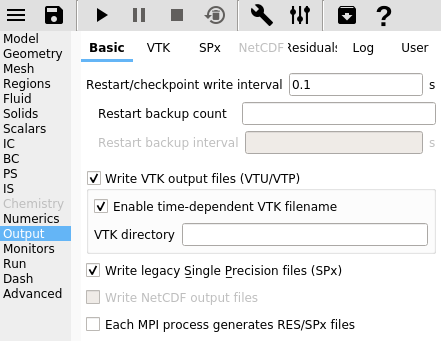
Select the
VTK
sub-paneSelect the “Background IC” region from the list to save all the cell data
Click
OK
to create the output
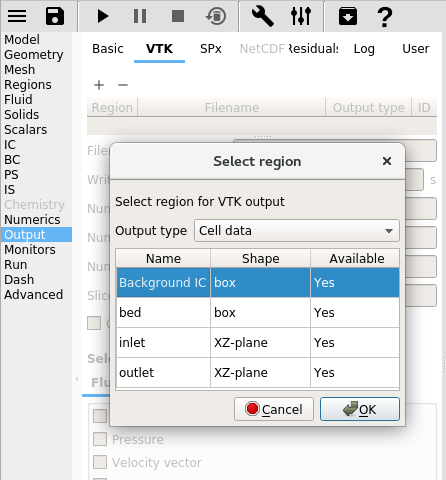
Enter a base name for the
*.vtu
files in theFilename base
fieldChange the
Write interval
to0.1
secondsSelect the
Volume fraction
,Pressure
, andVelocity vector
checkboxes on theFluid
sub-sub-pane
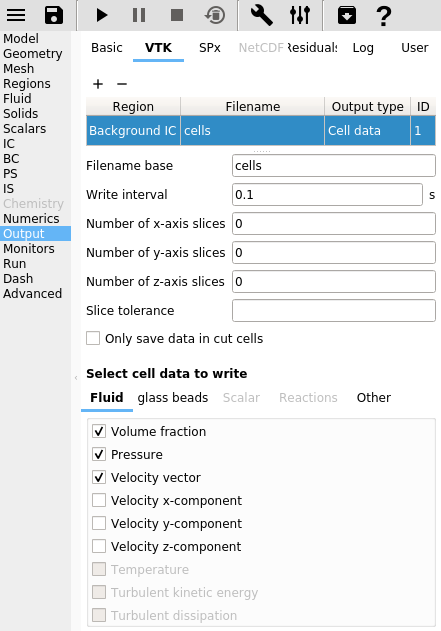
3.2.11. Change run parameters¶
On the Run
pane:
Change the
Time step
to1e-3
secondsChange the
Maximum time step
to1e-2
seconds
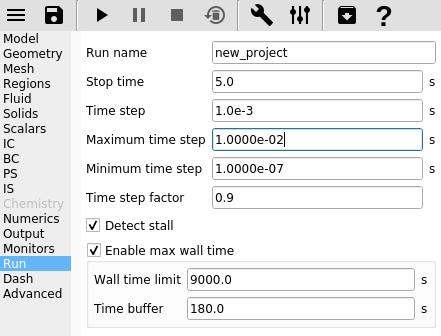
3.2.12. Run the project¶
On the
Run Solver
dialog, select the executable from the combo-boxClick the
Run
button to actually start the simulation
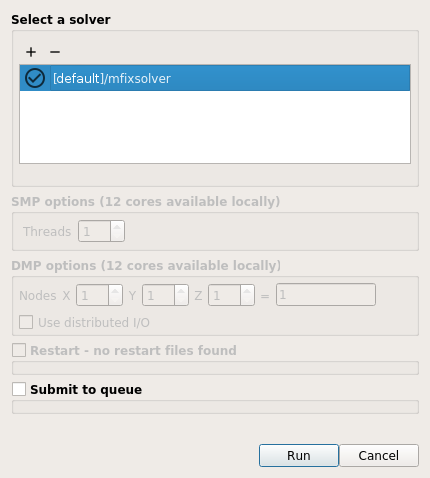
3.2.13. View results¶
Results can be viewed, and plotted, while the simulation is running.
Create a new visualization tab by pressing the
next to the Model tab
Select an item to view, such as plotting the time step (dt) or click the
3D view
button to view the vtk output files.
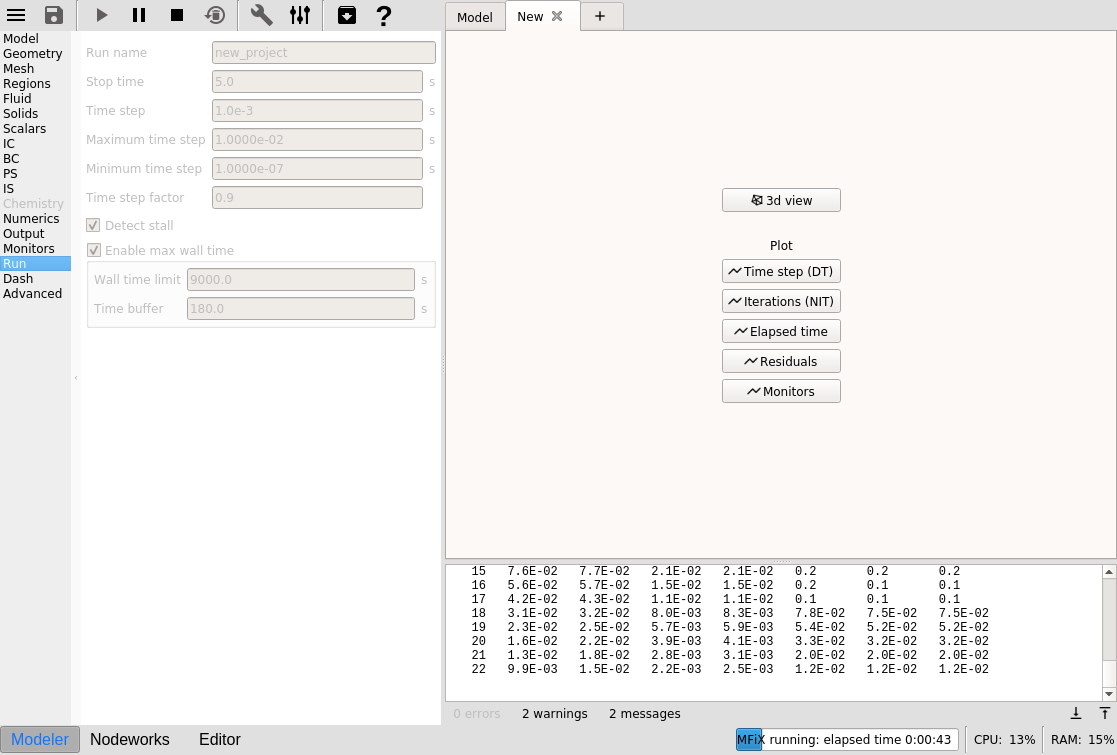
On the
VTK
results tab, the visibility and representation of the*.vtk
files can be controlled with the menu on the side.
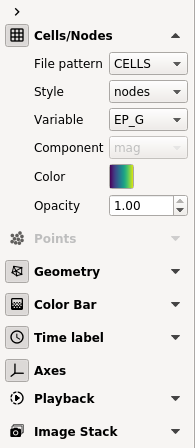
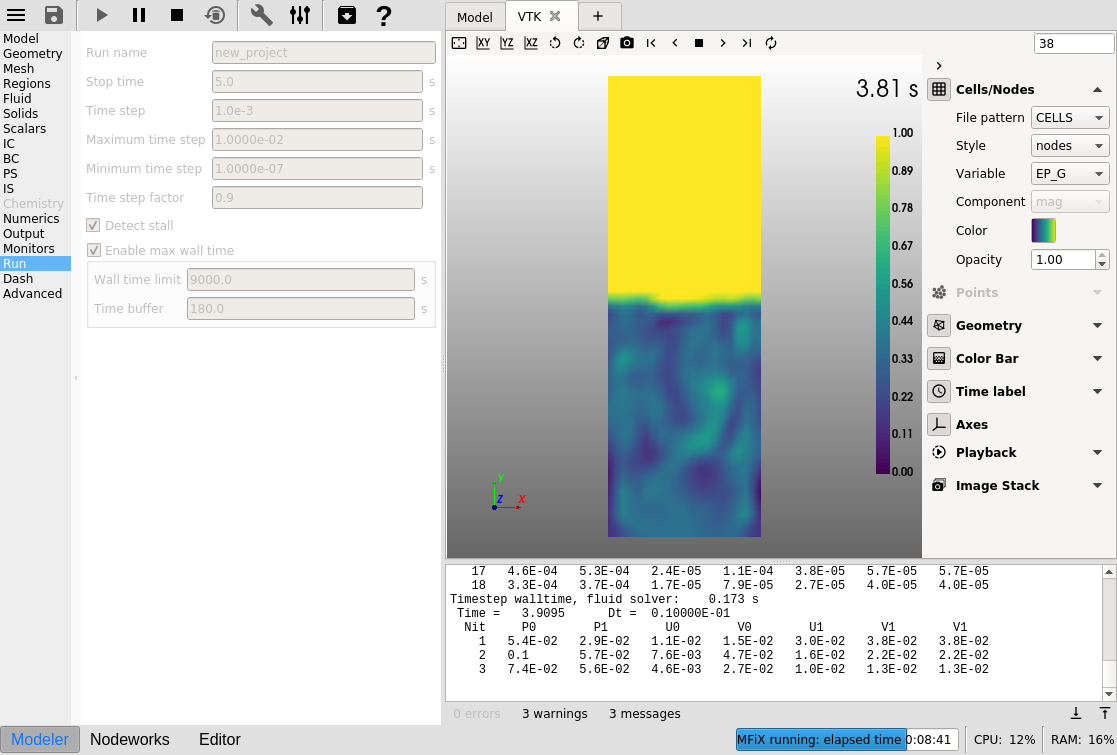
3.2.14. Increase grid resolution¶
For this simulation, increasing the grid resolution will better resolve the bubbles (at the expense of a slower simulation time). To do this: