3.7. DEM granular flow chutes¶
This tutorial shows how to create a three dimensional pure granular flow simulation from a series of cylindrical chutes. The model setup is:
Property |
Value |
---|---|
geometry |
1.75 m x 0.94 m x 0.2 m |
mesh |
20 x 20 x 10 |
solid diameter |
12.5 mm (0.0125 m) |
solid density |
2500 kg/m2 |
temperature |
298 K |
pressure |
101325 Pa |
3.7.1. Create a new project¶
On the main menu, select
New project
Create a new project by double-clicking on “Blank” template.
Enter a project name and browse to a location for the new project.
When prompted to enable SMS workflow, answer No, we will use the standard workflow for this tutorial.
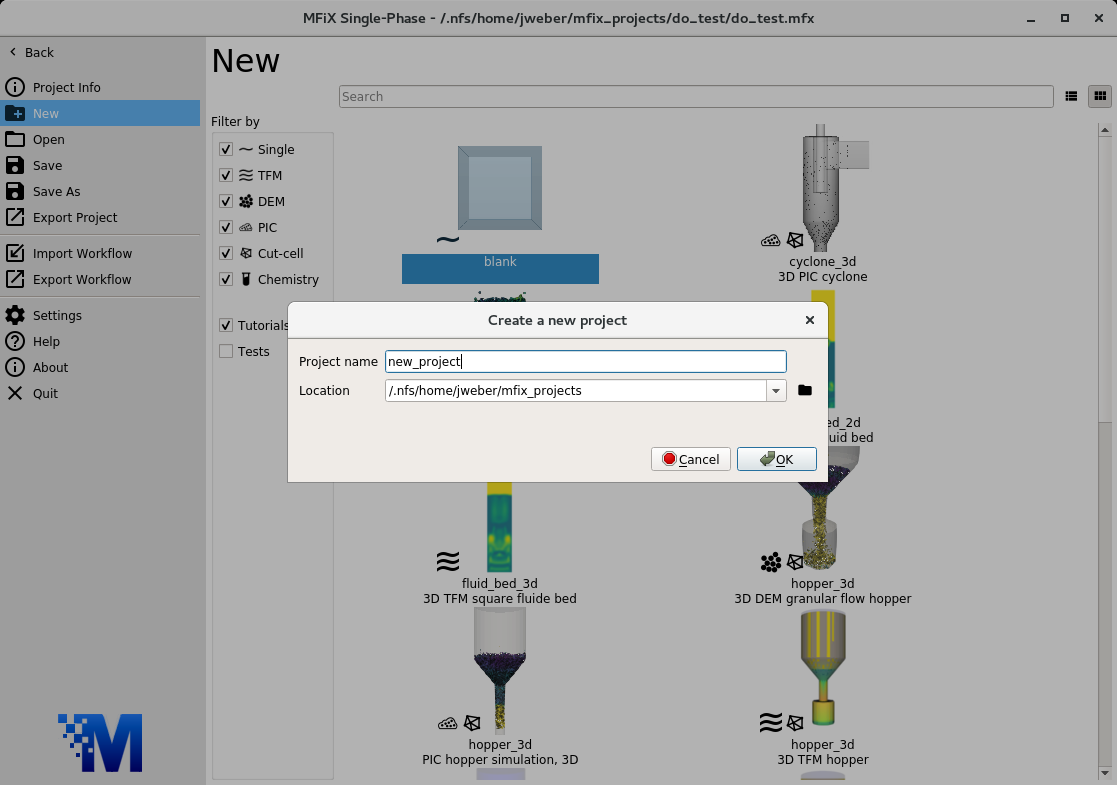
3.7.2. Select model parameters¶
On the Model
pane:
Enter a descriptive text in the
Description
fieldSelect “Discrete Element Model (MFiX-DEM)” in the
Solver
drop-down menu.Check the
Disable Fluid Solver
checkbox.
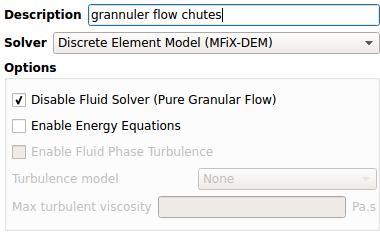
3.7.3. Enter the geometry¶
On the Geometry
pane:
Create the cylindrical geometry by pressing
->
primitives
->cylinder
Enter
0.1
meters for the cylinder radiusEnter
30
for the cylinder resolution
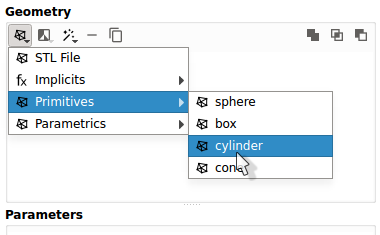
Create another cylindrical geometry by pressing
->
primitives
->cylinder
Enter
1.2
meters for the cylinder heightEnter
0.08
meters for the cylinder radiusEnter
30
for the cylinder resolution
Subtract the smaller radius cylinder from the larger radius cylinder
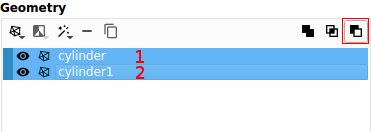
Slice the tube in half:
Change the
Center X
value to0.5
mChange the
Y Length
to1.2
m
Rotate the chute:

Copy the chute by pressing the
button with the chute selected (named
transform
)Enter a value of
0.8
in theTranslate X
fieldEnter a value of
0.6
in theTranslate Y
fieldEnter a value of
120
in theRotation Z
field
Copy the chute again by pressing the
button with the chute selected (named
transform1
)Enter a value of
0.0
in theTranslate X
fieldEnter a value of
0.3
in theTranslate Y
fieldEnter a value of
70
in theRotation Z
field
Press the
Autosize
button to fit the domain extents to the geometry
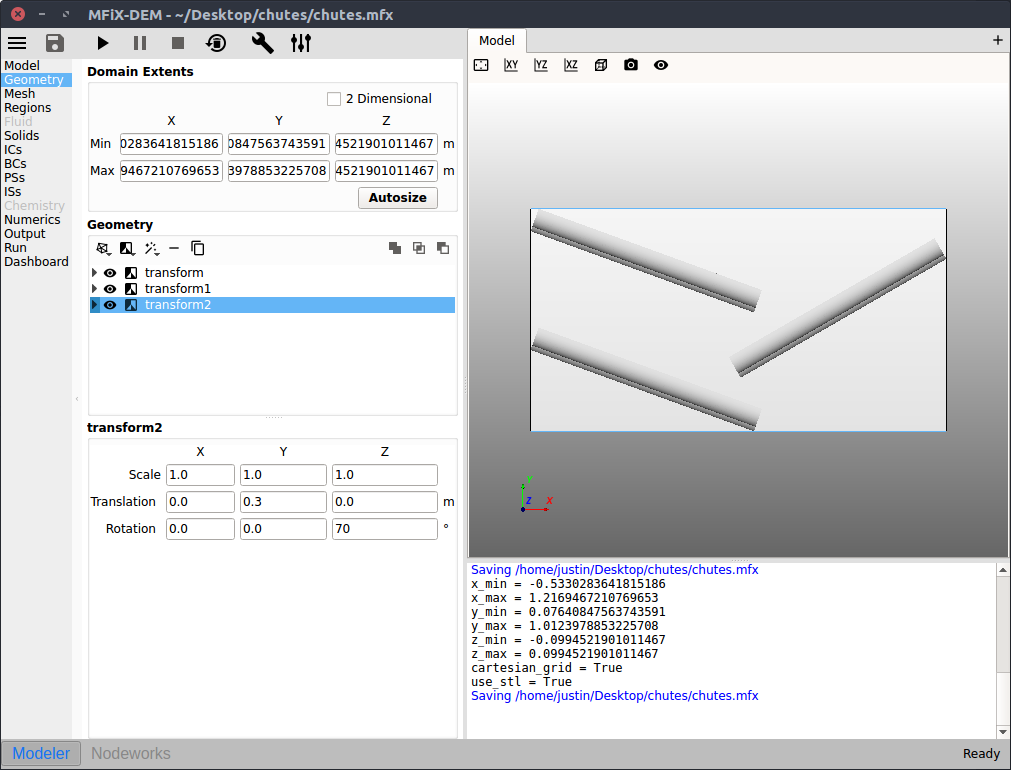
3.7.4. Enter the mesh¶
On the Mesh
pane:
On the
Background
sub-pane
Enter
20
for the x cell valueEnter
20
for the y cell valueEnter
10
for the z cell value
3.7.5. Create regions for initial and boundary condition specification¶
Select the Regions
pane.
Create a region to be used for the wall boundary condition
Create a region to be used as the mass inflow boundary condition
3.7.6. Create a solid¶
On the Solids
pane:
Enter a descriptive name in the
Name
field (“glass beads”)Enter the particle diameter of
1/80
m in theDiameter
fieldEnter the particle density of
2500
kg/m2 in theDensity
field
On the DEM
sub pane:
check the
Enable automatic particle generation
checkbox and keep defaults values for all other settings.
3.7.7. Create Initial conditions¶
On the Initial conditions
pane leave the default initial condition.
3.7.8. Create Boundary conditions¶
On the Boundary conditions
pane:
On the
Select region
dialog, select “Mass Inflow” from theBoundary type
drop-down menuSelect the “inlet” region and click
OK
On the
glass beads
sub-pane:Enter a value of
0.1
in thevolume fraction
field.Enter a velocity in the
Y-axial velocity
field of-0.1
m/s
On the
Select region
dialog, select “No Slip Wall” from theBoundary type
combo-boxSelect the “walls” region and click
OK
3.7.9. Select output options¶
On the Output
pane:
On the
Basic
sub-pane, check theWrite VTK output files (VTU/VTP)
check boxSelect the
VTK
sub-paneSelect
Particle Data
in theOutput type
combo box.Select the “Background” region from the list to save all the cell data
Click
OK
to create the outputEnter a base name for the
*.vtp
files in theFilename base
fieldChange the
Write interval
to0.1
secondsSelect the
Diameter
andTranslational Velocity
check boxes.
3.7.10. Run the project¶
3.7.11. View results¶
Results can be viewed, and plotted, while the simulation is running.
Create a new visualization tab by pressing the
in the upper right hand corner.
Select an item to view, such as plotting the time step (dt) or click the
VTK
button to view the vtk output files.
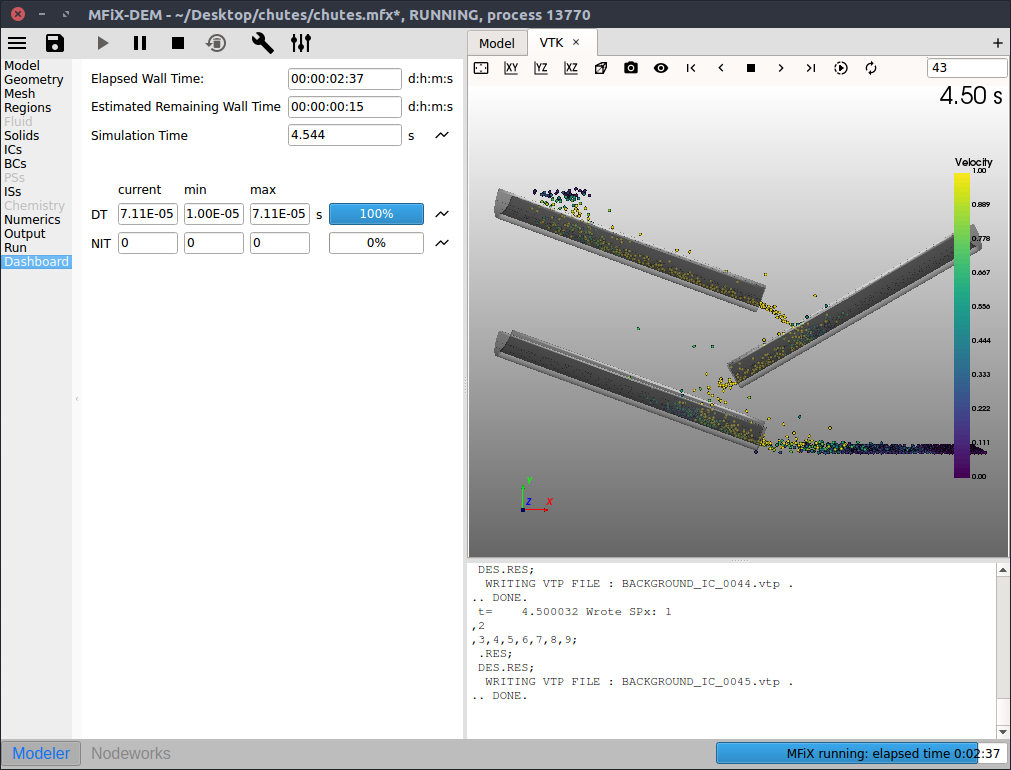