Home » Research
Research
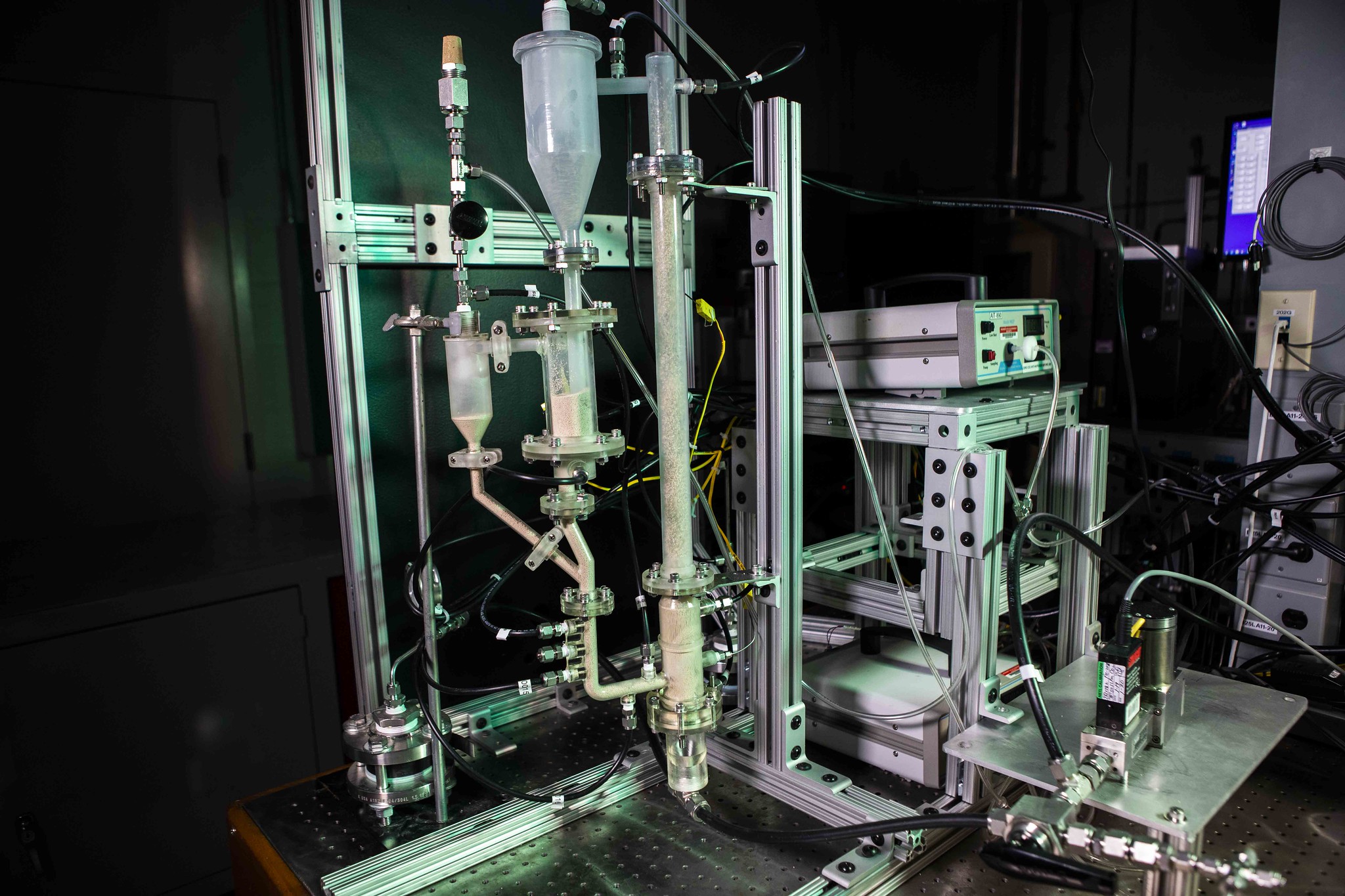
Multiphase Flow Science (MFS) research and development at NETL is funded by the U.S. Department of Energy (DOE), primarily from the Office of Fossil Energy and Carbon Management (FECM) with additional support from the Office of Energy Efficiency and Renewable Energy (EERE) and the Office of Science. The research work sponsored by DOE emphasizes the fundamental development of the MFiX Suite of software and associate software tools. These tools are then used to study of energy and environmental applications including gasification, carbon capture using solid sorbents or liquid solvents, and chemical-looping combustion of gaseous and solid fuels, circulating fluid bed combustion, biomass pyrolysis, catalytic processes, etc. that are important to DOE and the nation’s energy and environmental well-being.
Fossil Energy Program
MFS support of DOE’s Office of Fossil Energy and Carbon Management (FECM) is focused on FE’s mission to ensure the nation can rely on traditional energy resources for clean energy while enhancing environmental protection. MFS research at NETL is sponsored by the following FE Clean Coal Research Programs:
- Advanced Energy Systems – Including Gasification Systems, Coal FIRST, Transformative Power Generation and Coal-Biomass to Liquids;
- Crosscutting Research – Simulation-Based Engineering
The MFS team works to improve the understanding of both fundamental multiphase physics and the performance of multiphase devices that underpin technologies used in these research programs.
In NETL’s Advanced Energy Systems Programs, MFS research supports the Coal FIRST program, Transformative Power Generation, Gasification Systems, and Coal-Biomass to Liquids. These energy technology areas have many multiphase flow challenges to address, including:
- Complex homogeneous and heterogeneous chemistry for coal, biomass, metal oxide oxygen carriers, and catalytic materials;
- Multiphase flow regimes spanning packed bed to dilute transport, often in the same device;
- Multiple modes of heat transfer at high temperature including radiation;
- Broad range of particle sizes and densities;
- Complex particle-particle and particle-boundary interactions including attrition and agglomeration;
In the Crosscutting Research Technology Areas, MFS research supports simulation-based engineering activities in the Modeling, Simulation and Analysis program. Crosscutting Research provides multiscale, simulation-based engineering tools to accelerate development and deployment of FE technologies. In this role, this program supports the ongoing development and enhancement of the MFiX Suite of Software and associated software tools.
Energy Efficiency and Renewable Energy Program
MFS support of DOE’s Office of Energy Efficiency and Renewable Energy (EERE) is focused on FE’s mission to create and sustain American leadership in the transition to a global clean energy economy. MFS research at NETL has sponsorship from EERE’s Bioenergy Technology Office (BETO).
EERE’s Bioenergy Technologies Office (BETO) is tasked with developing technologies for producing cost-competitive advanced biofuels from non-food biomass resources, including cellulosic biomass, algae, and wet waste (e.g., biosolids). NETL is collaborating within a team of 6 national laboratories to support BETO programs under the Consortium for Computational Physics and Chemistry (CCPC). The CCPC brings together ORNL, NREL, ANL, PNNL, NETL, and INL to form a national laboratory consortium working to address challenges faced when using biomass feedstocks in renewable energy processes. NETL’s contribution is in the use of MFS tools – primarily the MFiX Suite – and applying multiphase flow and reactor design skills in the development and optimization of biomass reactors – including biomass pyrolysis reactors, catalytic upgrading of bio-oil, etc. The CCPC efforts support the BETO Chemical Catalysis for Bioenergy (ChemCatBio) consortium and the BETO Feedstock-Conversion Interface Consortium (FCIC).
Office of Science Program
MFS support of DOE’s Office of Science (SC) is focused on SC’s mission to to deliver scientific discoveries and major scientific tools to transform our understanding of nature and advance the energy, economic, and national security of the United States. MFS research at NETL has sponsorship from SC’s Advanced Scientific Computing Research program (ASCR).
SC’s Advanced Scientific Computing Research program (ASCR) is tasked with helping to maintain U.S. leadership in supercomputing, high-end computational science and advanced networking for science. MFS is supporting the ASCR’s Exascale Computing Project in the development of the MFiX-Exa code.
Research Structure
The MFS Research and Development program can be divided into 3 main classifications.